I was at a manufacturing conference in Toronto a few years ago and was fortunate to stumble across a presentation being given by Michael Abrashoff, retired U.S. Naval Captain and author of It’s Your Ship: Management Techniques from the Best Damn Ship in the Navy.
When Captain Abrashoff took command of the USS Benfold in 1997, the ship had one of the poorest service records in the U.S. Navy. One year later the crew of the Benfold achieved the highest performance ratings in the fleet—and went on to win multiple awards and achievements.
The details of this remarkable turnaround are well worth the read, but that day he told one story in particular that always stuck with me…
Sewage.
During the first 30 days of his new command, Captain Abrashoff spent most of his time exploring the ship, and one of the lessons he learned was that he had a sewage problem.
In the lowest part of the ship, in the dark of the bilge, there are pumps that move the ship’s sewage. It seems like such a meaningless thing—sewage pumps. This is a fighting ship of the sea, outfitted with the latest technology that the U.S. defense industry can attach to a floating vessel with the purpose of blowing other things up.
But the sewage pumps were junk. And they were junk in all of the ships of this class. So there was a shortage of parts to keep them running. And—as these things always go—there was a shortage of engineers who knew how to keep them running.
No big deal, these are just sewage pumps. They have no impact at all on the ship’s capacity to launch missiles.
But if these pumps are not functional, the ship is not combat ready. No sewage pumps, no operations.
So, Captain Abrashoff, recognizing the importance of these pumps, but more importantly, recognizing the importance of the sailors who kept them running, would make the difficult climb down into the depths of the ship to check on his staff—every day.
He could have just as easily picked up the phone and checked in, or had one of the ship’s officers do it for him. But he recognized the critical failure point that these pumps represented in his efforts to change the performance and culture of his command.
So, he took the time to personally visit these sailors so that they would clearly understand how important their work was to the success of the organization—every day.
Where Are Your Pumps?
You might lead a small team or a large company—either way, there are some great questions in this story:
Do you know where your “sewage pumps” are? Can you describe, right now, which functions or processes will stop your production in its tracks. Which ones seem vital, but under scrutiny, maybe aren’t so critical as you thought?
For food companies, the analogous “sewage pumps” are attention to food safety.
How much time do you devote to those things deemed ‘important’ by your managers that don’t add any value to actual accomplishment? Do you have the guts to ignore these for the good of your company and focus instead on what could make or break your business? Lack of attention to food safety, be it through sanitation or regular inspections, can cost you the business if you put increased production runs as the top priority.
Do you hide behind paperwork and reports, or do you climb down into the ‘bilge water’ at your plant? How often do you get out of your office and talk to the people who make your company actually work? Not the ‘junior officers’ and other middle managers, but the ‘coal face’ workers who make things happen? These individuals are the front line for food safety.
How important is prestige at your company? Does the value of the paycheck dictate the value of the individual? Does your culture acknowledge the importance of those who ‘do’ being just as (more?) important as those who ‘discuss’? It’s time to assess your operations and make sure that food safety is at the top of the priority list. Don’t risk the business.
Geoff Schaadt, M.Sc., MBA, is a consultant with Delta Partners.
Assessing Employee Food Safety Performance
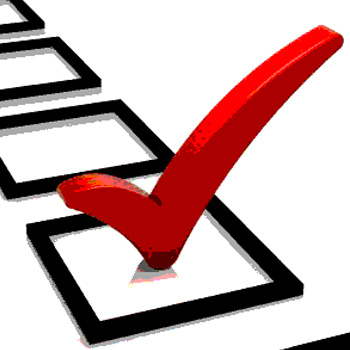